Arbeitsgebiete
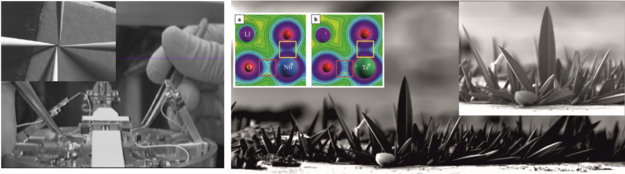
Kontaktpersonen
Prof. Raul Bermejo
Dr. Tanja Lube
Dr. Walter Harrer
Projekte in diesem Arbeitsgebiet
- Walzen II
- PTCCs und Varistoren
- Piezokeramik
- Layered Ceramics
- SICMAC - Structural Integrity of Ceramic Multilayers and Coatings
Kontaktperson
Schichtkeramiken wurden als alternative Wahl für die Konstruktion von Strukturkeramik mit verbesserter Bruchzähigkeit und mechanischer Zuverlässigkeit vorgeschlagen. Die Verwendung von Energiefreisetzungsmechanismen wie Rissverzweigung, Rissablenkung und / oder Rissgabelung kann die Risswachstumsbeständigkeit des Materials verbessern (Abb. 1). Die Verwendung maßgeschneiderter Druckeigenspannungen, entweder an der Oberfläche oder in den inneren Schichten, kann auch die Festigkeit sowie die Rissbeständigkeit des Materials während des Risswachstums verbessern. In dieser Hinsicht können Schichtarchitekturen, die mit hohen Druckspannungen ausgelegt sind, eine höhere Festigkeit und eine verbesserte mechanische Zuverlässigkeit aufweisen, was in einigen besonderen Fällen einen minimalen mechanischen Widerstand (Schwellenfestigkeit) ergibt, unterhalb dessen das Material nicht versagt.
In diesem Projekt werden Designparameter zur Optimierung der Festigkeit und Zähigkeit von Schichtkeramiken gesucht, die auf bruchmechanischen Analysen und Experimenten basieren. Es wurden zwei mehrschichtige Keramiken untersucht, die auf Aluminiumoxid-Zirkonoxid basieren und mit externen (ECS-Laminate) und internen (ICS-Laminate) Druckspannungen (Abb. 2) konstruiert wurden. Für jedes Design wurde eine optimale Architektur gefunden, die die Materialzähigkeit und -Festigkeit als Funktion der Geometrie und der Materialeigenschaften maximiert.
Unter Betrachtung der Toleranz gegenüber Defekten eignen sich ECS-Laminate für Keramikbauteile mit kleinen Rissen oder Fehlern, die in oder nahe der potenziellen Zugfläche des Werkstücks eingebettet sind. Andererseits legt das Vorhandensein großer Risse oder Defekte die Verwendung von ICS-Laminaten nahe, um eine zuverlässigere Reaktion zu erzielen. Diese Analyse kann auf andere Laminate ausgedehnt werden, die auf solchen Energiefreisetzungsmechanismen basieren.
Für ICS-Laminate wurde eine Mindestfestigkeit gefunden (Schwellenfestigkeit), die zu einem Rissstillstand in den Druckschichten führt (siehe Abb. 3). Dieses Verhalten kann mithilfe einer Gewichtsfunktionsanalyse erklärt werden, aus der hervorgeht, dass die verbleibenden Druckspannungen für die Zähigkeit des Materials verantwortlich sind, wobei die Druckschichten als Barriere für die Rissausbreitung wirken können.
Projekte in diesem Arbeitsgebiet
- PTCs
- Mechanische Zuverlässigkeitsanalyse von LTCC Bauteilen für die Automobilindustrie
- Integration von keramischen Bauteilen in Leiterplatten
- Walzen II
- Schichtkeramiken
- SICMAC - Strukturfestigkeit von Vielschichtkeramiken und Beschichtungen
- Federn
Kontaktpersonen
Fraktographie
Grundsätzlich werden fraktographische Untersuchungen verwendet um unerwartetes Versagen im Betrieb zu analysieren, ein Material zu verbessern und die Qualität eines Produktes zu untersuchen.
Spröde Werkstoffe versagen aufgrund von Defekten im Material (i. e. Volumenfehler wie Poren, Einschlüsse, Agglomerate usw.) bzw. Defekten an der Oberfläche.
Bei Oberflächendefekten handelt es sich hauptsächlich um Fehler die von der Oberflächenbearbeitung (i.e. Schleifen) stammen oder aber durch unsachgemäßes Handhaben der Bauteile und Proben in die Oberfläche eingebracht werden. Um derartige Defekte zu identifizieren werden nach Festigkeitsversuchen in der Regel fraktographische Untersuchungen durchgeführt.
Kontaktpersonen
Keramiken enthalten eine Vielzahl kleiner herstellungsbedingter „Defekte“, das sind Werkstoffinhomogenitäten, die zu einer lokalen Konzentration der Spannung führen. Diese „Defekte“ können als Risse beschrieben werden. Das Versagen von Keramiken geht in der Regel von so einem (dem bruchauslösenden) Defekt aus. Große Defekte verursachen geringe Festigkeitswerte. Das Griffith/Irwinsche Versagenskriterium sagt voraus, dass die Festigkeit mit dem Kehrwert der Quadratwurzel der Defektgröße skaliert. Da in geometrisch gleichen Proben die größten (bruchauslösenden) Defekte unterschiedlich groß sind, ist auch die Festigkeit der Proben verschieden: die Festigkeit weist eine große inhärente Streuung auf, die mit einer Verteilungsfunktion beschrieben werden kann.
Das Thema der Bruchstatistik keramischer Werkstoffe ist seit Gründung des Institutes ein zentraler Forschungsbereich. Grundlage der Tätigkeiten sind die Arbeiten von Danzer und Danzer et al., in der der grundsätzliche Zusammenhang zwischen der Fehlergrößenverteilung im Werkstoff und der Bruchstatistik von Proben beschrieben und erste Anwendungen dieser Erkenntnisse auf Werkstoffe mit Eigenschaftsgradienten dargestellt werden.
Bei den Arbeiten zur Bruchstatistik wird in der Regel eine große Anzahl von Proben unter definierten Bedingungen gebrochen, um daraus eine Verteilungsfunktion für die Bruchwahrscheinlichkeit als Funktion der Bruchspannung zu erhalten. Gut abgesicherte experimentelle Ergebnisse, die als Basis bruchstatistischer Theorien verwendet werden können, sind wegen der hohen Kosten für die Anfertigung von Proben praktisch nicht zu erhalten. Daher werden Festigkeitsverteilungen daher virtuell mittels Monte Carlo Simulationen erzeugt. So können typische Messwerte unter der Annahme „erzeugt“ werden, dass die „richtige“ Verteilung bekannt ist. Vergleiche zwischen simulierten und gemessenen Stichproben geben wichtige Aufschlüsse über das Werkstoffverhalten. Mit dieser Methodik wurden auch durch Simulation von Tausenden von Stichproben die Vertrauensintervalle der Weibull Parameter in Abhängigkeit von der Stichprobengröße ermittelt.
Weitere Arbeiten zeigen, dass es mit den in der Praxis üblichen Stichprobengrößen (etwa 30 Bruchversuche) nicht möglich ist, zwischen einer 2-Parameter und einer 3-Parameter Weibullverteilung zu unterscheiden. Es ist auch nicht möglich eindeutig festzustellen, ob eine Weibullverteilung, eine Normalverteilung oder eine Log-Normalverteilung vorliegt. Dazu müsste die Stichprobengröße wesentlich angehoben werden.